|
Wind Speed and windmills explained |
|
By Don Brown
The following article was sent to
Silicon Chip Magazine as a response to my first windmill
article. Don sent me a copy and I thought it was so
good I asked him if I could place it on my web site.
My congratulations to Glenn Littleford
for Part 1 of his December 2004 article in Silicon Chip
magazine on Windmill Generators. Like Glenn, they are
a topic dear to my own heart, and I have been tinkering
with them as a hobby over the last 15 years or so.
For the benefit of any of your readers inclined to experiment
with windmills (wind turbines, actually), there are
a few points that I have stumbled on that might be of
interest.
Tip Speed Ratio - this is the ratio between the
wind speed and the turbine blade tip speed, and is the
starting point for designing the turbine itself. The
optimum TSR band changes with the "solidity"
of the turbine disc (i.e. how many blades it has).
When operating at its design TSR, maximum power can
be extracted from the wind. As the actual TSR shifts
above or below its design point, the available power
decreases substantially. A turbine with a single blade
(and a counter weight on the other side) might be designed
for a TSR of 10 to 15. As you add blades, the optimum
TSR decreases, and a 3 blade turbine will work most
effectively with a TSR in a band between 4 to 7. The
typical multi-blade farm "windmill" pump operates
at a TSR of less than one. For a 3 blade turbine with
a 2 metre diameter and a TSR of 4.5 in a 5 metre per
second wind, the optimum tip speed would therefore be
5 X 4.5, or 22.5 metres per second. This translates
to a turbine shaft speed of 215 rpm. For a 20 metre
diameter turbine, the rotational speed would be only
21.5 RPM to maintain the same TSR. These low speeds
do not suit most alternators or generators and, in the
case of the 20 meter turbine, would certainly require
stepping up by a gearbox.
Note also that, if the wind speed doubles, then the
turbine speed must double to permit maximum power to
be extracted.
Power in the wind and power extraction - As a rough rule of thumb, you would require an 8 metre
diameter turbine to extract 1 kilowatt of power from
a 5 metre per second wind (18 kph). This assumes that
the turbine is 30% efficient. According to a Mr. Betz,
you can actually only extract 60% of the wind energy
anyway.
The power available in the wind varies as the cube of
the wind speed (sorry Glenn, a point of disagreement
here), and as the square of the turbine diameter. This
means that, for even minor wind speed increases, there
is an enormous increase in extractable energy. In most
locations, though, wind speeds tend to be low, and the
art with turbines focuses on extracting useful energy
at the prevailing (usually low) wind speeds. Any small
increase in wind speed can provide substantial power
dividends so, within reason, the higher you can mount
your wind turbine the better. Your local council and
the neighbours may, however, not share your enthusiasm.
Blade Twist or Helix- There is
a lot of science in efficient blade design, and I don't
pretend great expertise. The principle of blade twist
is, however, relatively simple. Air arriving at the
leading edge of a turbine blade hits the blade with
the speed of the wind in an axial direction, while the
blade simultaneously hits the air at its circumferential
speed. The circumferential speed depends on the radius
of the point in question from the turbine axis, and
is obviously fastest at the tip.
Considering the tip for the moment, if it is operating
at its design TSR, then the air hitting the tip will
do so at an angle to its rotational plane which is the
angle who's cotangent is the TSR (see Figure 1). If
the TSR is 4.5, then this angle is 12.5 degrees to the
plane of rotation. At half the diameter, where the speed
ratio is half, the angle is the cotangent of half the
TSR (or, in this case, 23.9 degrees). The attached table
gives the twist angles for various percentages of the
radius of a three bladed turbine with a TSR of 4.5,
but can be readily recalculated for other TSRs.
Note that the twist angle is not directly proportional
to the radius, but follows the cotangent function. The
rate of twist increases closer to the turbine axis.
Aerofoils - At high wind speeds
there is so much wind power available that even bits
of packing case timber set at an angle to the wind can
generate power. The art is in efficiently extracting
power at low wind speeds. Efficient turbines use aerofoil
sections, like those used for the wings and propellors
of aeroplanes.
All aerofoils can be distinguished by having a lifting
side, where the air moves more quickly than on the other.
The lifting side is ordinarily convex, while the other
side may be identical, less convex, flat, or even concave.
A turbine blade is no different to an aerofoil wing
or propellor in its use of one (or several) aerofoil
shapes. One essential difference though is that a turbine
blade needs its lifting side away from the wind, while
a propellor blade has it towards the direction of travel.
One of the things which distinguishes one aerofoil shape
from another is its lift to drag (L/D) ratio. Lift is
the force exerted at right angles to the incident air,
while the drag force is in the same direction as the
incident air. Really excellent aerofoils can produce
a lift force of around 100 to 150 times the drag force,
although values of around 20 are more readily achievable.
Attainment of high orders of L/D ratio are
very much dependent on accurate reproduction of the aerofoil
design, and a very high standard of finish. There are dozens
(hundreds, probably) of aerofoil sections that have been developed
by bodies such as NACA (now NASA), and their development is
a science in itself.
A table enabling the venerable NACA Clark Y aerofoil to be
set out is attached (Table 1). Being essentially flat on the
lower face, the Clark Y is a relatively simple shape to reproduce,
and has been used for many aeroplane propellors.
It is, however, by no means the ultimate wind turbine aerofoil.
Its low L/D of about 20 needs a TSR at the lower end of the
band (which is why 4.5 has been used as the example value)
and lowers the turbine efficiency. The aerofoils of most interest
to wind turbine blade experimenters chasing higher L/D ratios
and hence efficiency tend to come from the lower speed end
of the range, as developed for model aeroplanes. This is to
do with having a similar Reynolds Number, to the turbine operating
conditions (for those interested in following up the matter).
Erosion, or an accumulation of lumps from insects (particularly
over the first third of the lifting surface), spoils the air-flow,
and substantially lowers the L/D ratio. Glenn's comments on
the need for initial and ongoing attention to this matter
should be noted.
Angle of Attack. The angle between
the incident air and the aerofoil chord (line between the
leading and trailing edges) is called the Angle of Attack.
As a rule of thumb, the highest lift is developed at an angle
of attack of about 10 to 12 degrees to the incident air. The
point of stall, where the air flow detatches from the lifting
side and the lift collapses, occurs at an angle of about 16
degrees. The AA that provides the highest Lift to Drag ratio
is the angle of most interest to aeroplane designers, and
occurs somewhere between 0 to 4 degrees, depending upon the
aerofoil selected.
Wind turbine designers are primarily interested only in the
component of the lift that provides torque in the plane of
rotation of the turbine, and may select a higher AA to get
more lift. The component of lift acting in the same direction
as the actual wind only serves to load up the support tower
(see Figure 2), so turbine and aeroplane designers have different
views on lift. |
Turbine Blade Angle - For best efficiency,
a turbine blade needs to be set at the twist angle minus the
desired angle of attack (i.e. the blade angle - see Figure
1). Suggested blade angles for a percentage of blade radii
for a typical three-blade turbine with a TSR of 4.5 are given
in the Table 2. This is based on an arbitrarily selected AA
of 4 degrees, but this can be the subject of some experimentation
(in association with different aerofoils). The AA does not
need to be constant for all of the blade length (nor does
the aerofoil section), and this is a fertile area for the
experimenter to research.
It is interesting to note that, if the blade was being designed
as a propellor, the angle of attack would be added to the
twist angle. This is because, for a propellor, the concave
side of the aerofoil is on the opposite side to that for a
turbine blade. Thus, while a propellor with something like
the right tip blade angle might be pressed into service for
a wind turbine, it is not really designed for this task, and
will not extract wind power as efficiently (unless designed
with an AA of zero).
It should be noted that some studies have shown that it is
possible to achieve good wind turbine blade performance without
twisting the inner part of the blade, due to a phenomenon
described as "stall delay". What this means is that
the inner portion of the blade has been found to be contributing
useful torque, even though the angle of attack to the theoretical
incident air exceeds 16 degrees. This is probably due to the
more complex air flows associated turbine blades, which wing
theory does not accommodate.
While an untwisted blade would be simpler to set out, it will
certainly be less inclined to self-start (see below), and
may not be worth the trade-off.
Blade taper and thickness - There are
both aerodynamic and mechanical reasons for tapering the blade
(ie reducing the width) towards the tip. Both relate to square
law effects. As the width (chord) decreases, the thickness
needs to reduce at least in proportion.
The lift generated by any element of a turbine blade is proportional
to the chord, and the square of the incident air velocity.
If the width, or chord, remained constant, then the blade
tip would develop four times the lift of the centre of the
blade, and might bend.
The force tending to cause parts of the blades to break off
is also proportional to the square of the rotational speed.
If the mass of the blade tip is lower, then the inner parts
of the blades do not need to be as strong.
In addition to tapering the blade chord towards the tip, blade
thickness (perpendicular to the chord) is generally increased
towards the centre. This does not have much adverse aerodynamic
effect, but certainly creates stronger blade sections towards
the root.
Overspeed and blade forces - Because
of the huge increase in wind power as the speed increases,
wind turbines can spin to destruction even if loaded to the
maximum extent capable from the alternator. As noted above,
the force trying to rip the blades out of the hub increases
with the square of the rotational speed. To put some dimension
to this, a 2 metre diameter blade weighing 4kg and rotating
at 1,200 RPM develops a centrifugal force of about 3 tonnes.
Even if only part of a blade breaks off, the resulting out
of balance rotation of what remains will quickly destroy the
generator and support structure,
This is an argument for keeping the blades as light as possible,
yet strong. Wood (particularly the less dense but straight
grained type) is still a very suitable choice for this. You
probably can't get into too much trouble with a turbine of
up to a metre or so in diameter, but don't go for broke regarding
size till you get some experience with smaller ones, or you
might do just that.
Some wind turbines use pitch changing or wind spill techniques
to safeguard the blades, while others rely on brakes, or strength,
or mutual air disturbance by the blades to limit the ultimate
rotational speed. Even a piece of rope hanging from the wind
vane can permit the turbine to be turned out of the wind if
all else fails.
As someone who has been there, my strong advice is, don't
expose your turbine to the wind until you have a way of stopping
it when you need to.
Balance - Because of the substantial
centrifugal forces that can develop, the turbine must be well
balanced. The simplest way to do this is to take a nut and
bolt of the same diameter as the turbine shaft, and to drill
a small hole through the exact centre of the bolt. A piece
of string or fishing line is then fed through the hole, and
the turbine is suspended with the blade horizontal.
The nut is then used as the "sensitivity" setting
(Figure 5)
The closer the top of the bolt comes to the centre of gravity
of the turbine, the more sensitive the balance adjustment
becomes. Pieces of paper can be used as test weights to verify
that accurate balance has been achieved. Pick somewhere free
of drafts to check the balance
Blade attachments - Don't forget that
the most highly stressed part of a turbine blade will be the
root and its attachment point to the hub. This presents some
challenges for a 3 bladed prop. Be particularly careful to
avoid abrupt section changes or other stress raisers such
as holes in this area. Remember also that the centrifugal
forces produced by one blade are balanced by the other two,
and the hub design must provide adequate material section
for the transfer of these forces.
Fatigue - Because of pressure changes
due to wind masking by, say, the support tower, each rotation
of the turbine produces stress changes which can lead to ultimate
fatigue failure in some materials - notably aluminium. The
wind turbine has been described as a very good fatigue generator,
in addition to anything useful that it might do, so keep up
the inspections.
Rotational Hazard - Just like aeroplane
propellors, rotating wind turbines are dangerous, and must
be treated with caution. This is especially so in an over-speed
condition, where anything breaking off becomes a dangerous
missile. The apparently slow rotating turbines in a wind farm
kill birds, who apparently do not realise that the tips are
travelling at 5 or 6 times wind speed.
Starting - When the turbine is stationary,
the blades are in a deeply stalled condition, and require
a significantly higher wind speed that the minimum generating
wind speed to start rotating. This results in lost power generating
opportunities, and some generator controllers include a "bump"
facility to kick start rotation. Even a push helps.
Vibration and Noise - Turbines driving
a single phase alternator are inherently noisy. The situation
is much improved with a multi-phase alternator.
The blade tips can also generate noise, and some boat wind
generators are notorious for this effect. The answer probably
lies in an improved tip design, but I have no suggestions
to offer.
Proper balance of the turbine is also necessary to minimise
noise. Resonances in the support structure can occur, and
can be remedied by stiffening.
Conventional charging circuitry - A
typical wind turbine alternator connects to a (bridge) rectifier,
which then connects to the battery under charge (Figure 3).
Note that current can only flow from the alternator to the
turbine once its terminal voltage exceeds that of the battery
voltage, plus the diode bridge forward voltage drop. The current
waveform is therefore unlikely to be a clean sinusoid, and
some harmonics will be generated.
To minimise losses in the diodes, these should be of the Shottky
type with the lowest available forward voltage drop (so long
as they operate within their reverse voltage rating).
Conventional charging circuit shortcomings - As noted above, for the turbine to operate at maximum
efficiency, it must run at or near its design TSR. This requires
that its turbine speed must linearly follow the wind speed.
For alternators with fixed excitation, the no-load voltage
will be proportional to shaft speed.
The problem is that, with conventional circuitry, the alternator
is more or less locked to the battery voltage, and the turbine
will generally be operating below optimum speed as a consequence.
Switchmode charging circuit - In Figure
4, the alternator is connected via a switchmode charging circuit,
which can let the alternator operate at voltages significantly
above the battery voltage. The switchmode circuit works by
connecting the alternator DC output voltage to the battery
for a brief period. The current that flows is limited by the
inductor, which also stores energy in the form of a magnetic
field. When the switch opens, the polarity of the voltage
of the inductance reverses, and current flow is maintained
through the battery and the Shottky diode while the magnetic
field dissipates.
The current burst flowing into the battery is thus longer
than the current burst from the alternator side, while the
voltage is lower. As very little energy is lost in this process,
over a burst cycle, power in effectively equals power out,
and the system works as a DC transformer.
This permits the alternator to operate at a higher voltage
consistent with a higher turbine speed.
Open Loop Control - The switchmode
controller can be programmed to continually make an incremental
change to the alternator side voltage reference (ie shorten
the burst time to increase the alternator voltage level),
pause, and see if the current delivered to the battery increases.
If it does, then it makes a further incremental change, pauses,
and again checks the current. Should the battery current reduce,
it will decrement the voltage reference.
Using this technique, the maximum power available from the
alternator under any wind conditions can be tracked by letting
its output voltage (and hence turbine speed) rise or fall
to its optimum level. It should be pointed out that the wind
is never constant, so that the alternator side voltage is
always changing anyway.
I have built these controllers using analogue circuitry, and
have an unfinished one using a micro-controller. One day .....
Closed Loop Control - If the alternator
speed and the undisturbed wind speed are known, then the controller
can be set to maintain a constant ratio between the two. If
the wind should increase, the controller would shift to a
higher reference voltage consistent with the expected higher
turbine speed, thus unloading the turbine and assisting it
to accelerate to its expected speed.
If the wind speed drops, the voltage reference would lower,
loading up the turbine and recovering energy from it while
it slows to its new, more appropriate speed.
Wind Speed Sensing - Although it has
since sucumbed to the effects of UV and birds, I made a very
serviceable cup type anemometer out of three Andronicus coffee
measuring spoons. These drove an optical encoder built into
the case of a small DC motor shell with the magnetics and
brushes removed. I first tried a magnetic sensor, but found
that even the small cogging from the magnet interferred with
the operation.
Cup type anemometers are great because their wind speed characteristics
are linear, and their rotational speed is close to the wind
speed divided by the radius to the cup centre. This being
said, a reasonable size two bladed turbine driving an unloaded
DC motor used as a generator can serve satisfactorily and
with linear voltage output as long as it starts before the
power turbine. This will, of course, require a pivot and a
wind vane.
Note that the air stream upstream and particularly downstream
of the turbine is affected by the turbine itself. Air-speed
sensing needs to be at least 1.5 diameters ahead or to the
side of the turbine.
Alternator speed sensing - The simplest
way to do this is to set up a pulse counter to monitor the
alternator output frequency.
How much better? - As the wind is always
changing, it is difficult to measure the extent of any improvements
that you think that you have made unless you have access to
a wind tunnel. The solution is to have two units identical
in every respect except for the feature that you are testing.
By mounting them on a common pivoting support and exposing
them to an airflow that is as undisturbed as possible, they
should see more or less the same air-flow.
By measuring the amp-hours output from each into a common
load, the benefit of any enhancement can soon be checked.
Using the amp-hours check with no enhancements fitted will
also establish whether there is any difference before you
start testing.
By mounting two alternators on a common T shaped pivoting
bracket it is also possible to pivot and spring load them
such that they will automatically unload themselves in strong
winds (refer Figure 6).
Alternator suitability - This is the point where I am looking forward to Glenn's
next article.
As noted above, a 2 metre diameter turbine has a design speed
of about 230 to 300 RPM in a 5 metre/sec wind (depending on
its TSR). With this diameter turbine, at this wind speed,
it should be possible to recover 60W (or send 5 Amps into
a 12 volt battery). While it is certainly possible to design
an alternator that will do this, at this shaft speed, most
of the off the shelf devices would require a step-up gearbox,
or similar. Generally, a larger diameter alternator is needed
to produce useful power at low shaft speeds.
If the turbine diameter was reduced to 1 metre, then the shaft
could turn at 460 to 600RPM, which is just getting into the
ball-park. Unfortunately, though, the power extraction capability
drops to 15W (square law on the turbine diameter, remember)?
Like the turbine blade itself, producing a low speed alternator
to output, say, 5A at 14V at 300RPM is more fertile ground
for experimenters.
I hope that the above observations provide
a little additional interest for your readers in conjunction
with Glenn's articles, and may, perhaps, elicit some comments
from others. Wind turbines (OK, I confess to calling them
windmills too - even though they don't produce flour) are
great things to experiment with - especially when you have
an understanding of the basics. There is always a fascination
with getting something for nothing from the wind or the sun.
I would also point out that there is a wealth of information
out there on wind turbine design. Particularly recommended
grounding is The Wind Power Book by J Park (Cheshire Books).
Incidentally, I have been reading and enjoying
your magazine and its forebears since the days of "Radio
and Hobbies" magazine, which probably gives my age away
somewhat.
Keep up the good work.
Regards
Don Brown
Beachmere, Queensland
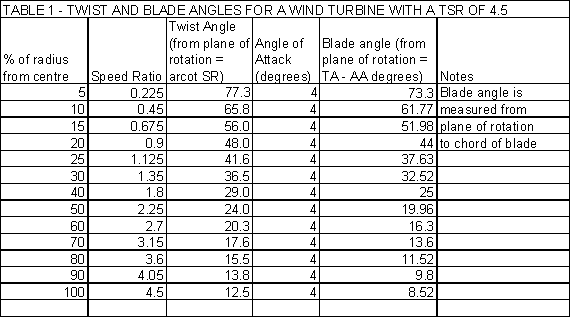
|