GWatPE
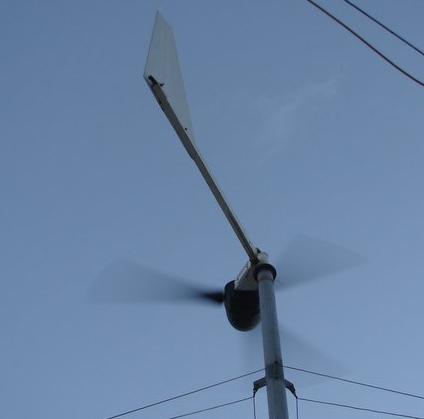 Senior Member
 Joined: 01/09/2006 Location: AustraliaPosts: 2127 |
Posted: 12:57pm 12 Mar 2008 |
Copy link to clipboard |
 Print this post |
|
Hi AllanS,
My first attempt of a winmill blade on my machine was single bladed. I had followed a line of thought from a propellor I adapted for my electric powered model aeroplane. Single blade propellors have been used in high RPM applications to increase efficiency by allowing the propellor blade to cut undisturbed air on each revolution. I started off with a 2.8" blade that rotated at 20,000RPM and made of solid carbon fibre with a moulded in lead counter balance to the hub. What I found with the scaled up windmill version was the counter balance was 4 kg heavier than the blade. The only way to reduce the weight was to move it out into the airstream. The mill head is a dynamic system with changes in rotor speed and rotor disk tracking changes with wind direction and degree of furl. I found that no matter how well balanced statically, harmonics were evident when the mill head changed direction. I scrapped the one and two blade prototypes and settled on a 3 blade. All of the dynamics balanced.
I started my testing a couple of years ago and I have had 3 blades[Lakota Carbon Fibre] flying for over 18 months. The single blade was unusual, but not practical.
The cost is probably related to economies of scale and labour in the manufacturing. I have designed my windmill for a long service life, so mechanical aspects were most important.
cheers, Gordon.
become more energy aware |
oztules
 Guru
 Joined: 26/07/2007 Location: AustraliaPosts: 1686 |
Posted: 03:45pm 12 Mar 2008 |
Copy link to clipboard |
 Print this post |
|
Hi AllanS,
I too have dabbled with the single blade concept. Like all things in this world, it has it's own advantages and disadvantages.
In simple terms that I can understand it goes something like this:
For a given wind speed and blade diameter, we have a given quota of power we can extract from the wind.
Suppose we have three blades giving X amount of power at Y rpm. The torque is distributed evenly among the three blades. if we add a fourth blade, we increase the surface area so our torque must increase, but for X to remain the same, the rpm must decrease to achieve the same power from the same airflow. ( the total power cannot go up for the same diam and wind speed)
So we end up with the same power at a slower rpm. For a given blade we can say more blades gives same power at lower RPM, less blades will give same power at higher RPM.
The biggest advantage with low blade count seems to be the higher rpm. With higher rpm we can use a smaller less cumbersome alternator, smaller magnets, and less turns of copper.
The downsides to a single blade (apart from looking odd) is that higher rpm has less run torque, less start torque. If you had cogging issues with the F&P with 3, 4, or 5 blades, you have no real hope with 1 blade. So iron loss style alternators would have a real problem getting out of stall.
The next problem is as Gordon describes above, yaw problems and instability when changing direction. This is a problem with 2 blades as well, and so 2 blades (whilst faster generally then 3) seem to be less popular than 3 blades because of this yaw instability. The balanced single blade yaws like a 2 blade (one blade being a weight out one side and a blade out the other..... really 2 blades for yaw purposes.)
The three blade arrangement seems to solve most of the competing requirements and compromises and so is the most used number. It is stable during yaw, gives fair rpm for diam and overcomes stalling sufficiently well to be useful and is structurally strong at high TSR.
Now ... to mess it all up.
Providing you build the blade profile to match a particular tip speed ratio, the number of blades should not matter with respect to speed. Torque per blade number will change but not the rpm at a given TSR..... This means we can use more blades, and we can keep the high RPM, but we need to decrease the blade surface area to decrease the torque per blade, so the power remains the same at that speed.....thinner blades for higher blade count.
However physical constraints with building thin enough blades to get high TSR with high blade count, means it is not practical to have high TSR with a high blade number and still have sufficient strength in the design to be reliable in heavy winds. (although Claus Nybroe's windflower (Windmission in Europe) uses 12 very thin blades at high efficiency but still a low (3.6)TSR.)
Hmmm... we come back to 3 blades being the best compromise between as high a speed we can get from physically strong blades without yaw problems.
So 1 blade will make power, possibly at higher RPM and so less alternator weight, but it's no free ride.
I never mounted mine on an alternator, but hand held (scared hell out of me) told me I had a serious yaw problem, and keeping the thing at right angles to the axis becomes a real problem when wind tries to force the blade backwards, but only on one side of the axis... no blade to push back on the other side is there, only a counter balance.... which does not catch the wind. So you can only realistically dynamically balance the thing if there is no wind to push the blade back.... which kinda defeats the purpose really.............
.......oztules Village idiot...or... just another hack out of his depth |